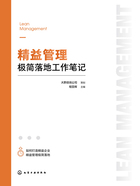
1.3 运营层面——消除“超负荷、浪费、不均衡”
1.3.1 交货的前提下,无限缩短产品的生产周期
为了赚取更多的利润,就需要更快地完成“销售—生产—交货”。如果销售速度很快,而生产周期很长,就必须备足成品库存,用于防止因此导致的销售断货。要防止断货,又不希望提前生产出成品而占用资金,就必须确保工厂的生产周期短于销售周期(消费者愿意等待的周期)。只有这样,才能在事前不生产库存的前提下,实现快速交货。如果生产周期过长,远远超出了消费者愿意等待的周期,就必然会产生库存。
或许有人会说:“如果生产周期没有办法缩短,我们把客户等待周期(交货周期)延长一点,大于生产周期不就行了。”但是,满足客户需求才能扩大销售,所以企业应尽可能地改善生产,匹配客户需求。
或许又有人会说:“缩短交货周期和生产周期的目的,就是让生产和交货周期短于供应商的付款周期,那我们直接把供应商的付款周期延长。”我们也不建议为了企业自身利益,把所有的成本都转嫁到供应商身上。利用企业自身的强势地位,强压供应商接受不合理的付款周期,这种做法虽然被很多大型企业用来转嫁成本,但并不是精益的思维。精益企业强调的是互惠互利,处于供应链上下游的企业之间,应当互相协同,一起服务好最终消费者。企业应当思考如何在改善自身状况的同时,协助提供服务的供应商进行改善,以建立强大、有保障的供应链体系。
企业接到订单后或者在客户需要交货时才启动生产,必须具备的前提就是生产周期短于交货周期。那么,如何缩短生产周期呢?生产周期能够最大限度地缩短到什么程度呢?
精益的思维,是将产品的生产周期,缩短到等同于产品的工艺加工周期。生产周期无限等同于产品的工艺周期,是缩短生产周期的核心。
产品是按照事先设定好的加工工艺流程制作出来的。一件产品从投料开始,不经过任何停顿,按工艺流程连续加工,直到变成最终的完成品,这个过程所花费的时间就是产品的工艺加工周期。严格意义上来说,工艺加工周期是按工艺改变原料物理形状和化学性质的各工序加工时间(cycletime,以下简称CT)之和。
产品的工艺加工周期=第1工序的CT+第2工序的CT +…… +最后完成品工序的CT。
需要注意的有两点:
(1)每个工序的CT,是以单件产品为单位测量出来的加工工时。
(2)工序间不存在排队等待的时间,一个工序加工完成,直接转到后一个工序,直至产品加工完成。
简单来说,产品的工艺加工周期就是单件产品的加工周期,最短的生产周期,意味着以一件产品为批量的流转加工,简称单件流(one piece flow)。
在精益的概念里,之所以要追求单件流,目的就是无限缩短生产周期,让生产周期等同于产品的工艺加工周期。
实现单件流必须具备的前提,一是完全按产品工艺流程的先后顺序,把所有的工序串联成连续不断的生产线。二是每个工序的加工批量,可以最小化到单件。事实上,受限于每个产品的加工工艺,很多企业很难具备这两个前提。但是致力于生产周期无限缩短,是精益改善必须持续坚持的追求。
企业在确保交货的前提下,无限缩短生产周期,目的就是不生产占用资金的库存。如果生产周期无限缩短,那么就可以实现在接到订单后才启动生产。实际上,生产周期不单单是产品的加工时间,还包括订单的处理时间(间接部门的事务处理时间)、生产的准备时间(工艺和物料的事前准备),以及上面提到的生产加工时间和成品出库后的货物运送时间。
如果只是站在工厂生产的角度来看,生产加工时间的缩短,就是尽可能实现上述的单件流,让产品的生产加工时间等同于产品的工艺加工时间。
站在经营的角度来思考,如果追求运营成本的最小化,实现1元赚100元的经营效果,就必须缩短图1-2所示四个方面的时间。

图1-2 实现1元赚100元的经营效果需节约的时间
精益企业的快速反应,需要在上述四个方面得到充分的体现。
如果希望在上述四个方面实现突破,实现革命性的改善,就需要对内部的运营流程进行全面、系统、深入的调查。
1.3.2 接单到交货的运营流程,消除其中所有不增加价值的无效工作
企业内的工作,受各项工作的制约,通常根据功能对部门和岗位进行精细分工,如图1-3所示。部门间跨越职能的工作联系,决定了企业的运营效率。如果期望实现运营投入最小化,使内部的运营周期短于客户对产品的需求周期,就需要对从接单到交货的全过程进行系统性的梳理,确保全过程的运营流程顺畅、连续、高效。从这个意义上来讲,打造精益企业等同于打造高效的运营系统。高效的运营系统始于客户(从客户下订单开始)、终于客户(到客户订单结束)。

图1-3 企业运营的简易流程
精益企业的高效运营系统,主要是对两个方面进行系统规划和改善,一个方面是从客户下单开始到物料采购订单下达到供应商的信息处理流程;另一个方面是从供应商送货开始到完成生产加工、成品出货的实物加工流程,如图1-4所示。对企业进行精益改善时,通常需要把当前的运营流程详细地调查出来,整体绘制在一张纸上,专业上称之为“物流与信息流图”。绘制物流与信息流图时,应把信息处理流程放在纸的上半部分,自右向左来绘制。把实物加工流程放在纸的下半部分,从左向右来绘制。通常可以选择一张A0幅面的白纸,上下对折,上半部分绘制信息处理流程,下半部分绘制实物加工流程(具体的绘制方法请参照第4章的内容)。

图1-4 信息处理流程和实物加工流程
打造精益企业,需要对信息处理流程和实物加工流程进行系统性的规划和改善。为了减少运营投入、缩短生产运营周期、提升运营效率,企业需要确保从接单到交货全过程的流畅,既要做到信息处理流程的顺畅,还要做到实物加工流程的顺畅。
1.3.2.1 实物加工流程
实物加工流程的顺畅,就是尽可能按照单件流的思想,把每个加工工序串联为生产线,使产品单件连续流动加工。即使无法做到把每个车间的每个工序都串联成生产线,也要考虑如何把每个车间的每个工序尽可能地无限靠近,减少工序之间的断点。把产品加工的每个工序尽可能地放在同一个物理空间内,有助于减少产品加工的环节,继而实现缩短加工周期的目的。
工序之间的断点越多,工序间存在的搬运现象就越多,为了提升搬运的效率,企业会希望增加每一次的搬运数量,这样一来,工序间就会产生(或停留)过多的中间库存。库存越多,占用面积就越大,工序间停顿、排队的时间就会增加,生产周期就会拉长。
所以确保实物加工流程的顺畅,就要尽可能地做到连线生产,消除工序之间的断点。没有断点就不会产生停顿,没有断点就没有中间库存,没有断点就不会产生搬运。
1.3.2.2 信息处理流程
信息处理流程的顺畅,需要在各间接部门之间,实现订单信息的快速流转。订单信息处理的每个环节,都要准确、快速,并且尽可能地不停顿。一个部门处理完该部门分担的任务后,要立刻转给另一个部门,避免在信息处理过程中有长时间的停留、等待和排队,从而实现信息处理流程的快速和高效。事实上,受限于每个事务部门自身的工作方式和习惯,部门间形成的壁垒,反而会造成信息处理的不及时,以及大幅度的延期和滞留。很多企业甚至出现“信息处理的周期远长于实物加工的周期”这样不合理的现象。
也有很多企业通过导入软件系统来实现信息处理的高效,实际上其带来的效果并不理想,问题在于在导入软件之前,没能对运营系统进行系统的梳理和规划。虽然导入软件之前,软件服务商会做事前调研,但由于过分关注软件的实施逻辑而非管理改善逻辑,通常达不到本文所提的目的。
信息处理流程的顺畅,在于打通间接部门之间的壁垒,清晰界定部门内的信息处理流程,以及部门间信息交接的方式(频度、时间节点、交接人)。如何确保信息在处理、传递过程中准确和不失真,是信息处理的关键。在缺少或未掌握系统、专业的改善方法之前,把各间接部门负责信息处理的人员聚集在一起办公,是一个简便有效的方法。
1.3.2.3 关注并消除运营流程中“超负荷、浪费、不均衡”现象
从接到客户下达的订单到完成生产交货,无论是信息处理流程还是实物加工流程,环节都比较多,如何打造精益企业,实现卓越、高效的运营呢?核心在于关注并消除运营流程中存在的“超负荷、浪费、不均衡”现象(见图1-5),这三种现象是客户需求和生产能力不匹配的具体表现。消除“超负荷、浪费、不均衡”的现象,目的在于追求生产能力和客户需求之间的极致匹配,实现均衡生产。

图1-5 造成成本损失的“3M”现象
接下来我们对三种现象进行详细说明。
(1)超负荷:日文为MURI,指的是生产能力小于客户需求。由于能力不足,难以满足需求,所造成的超负荷生产现象,需要临时增加设备和人力,提升生产能力,才能和客户需求相匹配。
(2)浪费:日文为MUDA,指的是生产能力大于客户需求,这时就会出现生产能力富余,富余产能则意味着浪费。
(3)不均衡:日文为MURA,指的是受客户需求变化的影响,有些工序能力不足(超负荷),有些工序能力富余(浪费);或加工能力时而不足、时而富余。
这三种现象(简称“3M”),都会导致生产成本的损失,所以企业务必致力于消除信息处理和实物加工过程中存在的这三种现象,追求信息处理流程和实物加工流程的极致均衡,达到既不会出现能力不足,又不会出现能力富余的“刚刚好”的状态。
消除3M现象,追求极致的均衡生产,应运用IE(industrial engineering,工业工程)生产线平衡的概念,追求生产状态的均衡和稳定,从而将生产运营成本降到最低。
均衡生产是实现“不多不少刚刚好”的产能和需求匹配,是企业应当极致追求的方向。实现均衡生产,需要对信息处理、产品加工进行系统的改善,实现生产方式的全面革新。企业追求均衡生产的过程,就是通过制造方法的改变实现制造成本削减的过程。这一理念涉及面广、改善课题众多,将在第2章进行详细介绍。