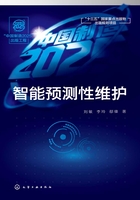
2.3 基于可靠性模型的故障预测方法
当设备系统的传感器数目较少或难以获得系统的物理模型时,在拥有大量历史失效数据的基础上,采用统计可靠性方法可以实现设备系统的故障预测。通过可靠性实验或相同类型产品使用过程中的故障数据拟合产品寿命分布,可以求得设备系统使用过程中的平均剩余寿命。如早期基于韦布尔分布、二项分布、指数分布等的可靠性分析,以及20世纪80年代中后期基于后验分布概率的贝叶斯方法等。基于可靠性方法使用范围较广,尤其适用于零批次多、数量大的商用产品,但精确度较低。
对于一般产品,可以通过对包含了失效故障的历史数据进行统计分析。最为经典的可靠性增长模型——杜安模型是J.T.Duane于1962年提出的,以图2.5所示的方式给出所度量的可靠性参数发生的变化,也能得出可靠性参数的数字估计,另外还有美国陆军器材设备分析机构提出的AMSAA方法。

图2.5 杜安模型
杜安模型假设可修产品的累积实验时间为t,在开发期(0,t)内产品累积失效次数为N(t)。产品的累积失效率λ ∑(t)定义为累积失效次数N(t)与累积实验时间t之比,即:

杜安模型指出,在产品研制过程中,只要对暴露的系统性失效不断地进行纠正和改进,使之不再发生,那么累积失效率λ ∑(t)与累积实验时间t的关系可以用双对数坐标纸上的一条直线来近似描述,数学表示式为:

即:

式中,λ ∑(t)为t时刻观察到的累积失效率;λI为估计的初始失效率,即在t=1时的失效率,也称为尺度参数,其几何意义是杜安曲线在双对数坐标纸纵轴上的截距;α为估计的可靠性增长率,其几何意义是杜安曲线在双对数坐标纸上的斜率。
表示累积失效率平稳下降的趋势由式(2.1)得到:

由式(2.4)可求出瞬时失效率与累积失效率之间的关系:

这样,瞬时失效率的估计值为:

因此,平均故障间隔时间MTBF的累积值θ∑(t)和瞬时值θ(t)可用下式求解:


基于对历史数据的统计分析,在获取一定统计样本的前提下,一般可以估计失效率或者故障率,来预测结果的准确度和精确度。最为典型的基于概率的预测方法是图2.6所示的韦布尔分布函数(又称浴盆曲线),该曲线是设备在运行寿命时间内故障发展的规律,表现为故障率变化的三个阶段,并对应故障分布的三种基本类型,即初始故障期为故障递减型、偶发故障期为故障恒定型、劣化故障期为故障递增型。

图2.6 韦布尔分布函数
第一阶段为初始故障期,也称为早期故障期,是指新设备(或大修好的设备)的安装调试过程至移交生产试用阶段。由于设计、制造中的缺陷,零部件加工质量以及操作工人尚未全部熟练掌握等原因,致使这一阶段故障较多,问题充分暴露。随着调试、排除故障的进行,设备运转逐渐正常,故障率逐步下降。
第二阶段是偶发故障期。这时设备各运动件已进入正常磨损阶段,操作工人已逐步掌握了设备的性能、原理和调整的特点,故障明显减少,设备进入正常运行阶段。在这一阶段所发生的故障,一般是由于设备维护不当、使用不当、工作条件(负荷、温度、环境等)劣化等原因,或者由于材料缺陷、控制失灵、结构不合理等设计、制造上存在的问题所致。
第三阶段是劣化故障期,也称耗损故障期。设备随着使用时间延长,各部分机件因磨损、腐蚀、疲劳、材料老化等逐渐加剧而失效,致使设备故障增多,生产效能下降,为排除故障所需时间和排除故障的难度都逐渐增加,维修费用上升。这时应采取不同形式的检修或进行技术改造,才能恢复生产效能。如果继续使用,就可能造成事故。
采用韦布尔分布描述对象元件的寿命分布特性,按照历史数据样本初始化获得一定的分布参数模型,然后再根据实际使用和操作过程中状态数据的变化(环境条件、负载条件等),动态估计韦布尔寿命分布参数变化,以此预测对象元件的剩余使用寿命RUL及其概率分布函数PDF。
自20世纪60年代提出了以可靠性为中心的维护理论以来,对于复杂设备故障,除了浴盆曲线故障模型外,还有图2.7所示的其他五种故障模型[10]。其中,故障概率呈稳定或缓慢上升的三种类型[如图2.7(d)~(f)所示]占了故障总概率的89%,其余的占11%。

图2.7 常见的故障分布函数模型
然而,基于可靠性模型的故障预测方法是建立在大量样本可靠性实验基础上的,对于类似于航天器、飞机等复杂昂贵的设备和系统并不适用。尤其是针对个体样本的健康状态评估,这种方法无法考虑诸多复杂因素,如运行环境、历史状态、退化特性等,预报的虚警率较高。