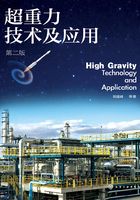
2.4 旋转填充床内气液传递过程与传质模型
2.4.1 液相控制的传质过程
早期的研究者,如Keyvani[14],Kumar[15]曾用旋转填充床对CO2-H2O系统的体积传质系数进行了研究。由于当时缺少有关液膜厚度和液滴直径等方面的研究,所以只能将KL和a一起处理,求出床层的平均液相体积传质系数KLa。虽然有的研究者将KL与a分开,得到单独的KL,但只是简单地把填料表面积看作传质面积,这与实际不符。
Munjal[8]用实验方法测定了相界面积,从实验得到了KL值。同时,他将液体在填料层中的流动简化为液体在旋转桨叶和旋转圆盘上的流动,利用溶质渗透理论求出了这两种情况下的KL值,但他未考虑填料空间的液体形态与传质作用。
北京化工大学超重力工程研究中心[9,13]对用氮气解吸水中氧的液膜控制传质过程进行了研究,还对逆流床的端效应进行了研究[1,26,27],结果表明,转子中填料的内缘(即端效应区)的传质系数很大,气液传质过程在填料层中主要发生在靠近转子填料内径的区域。
北京化工大学超重力工程研究中心[28,29]对以黄原胶水溶液为对象的拟塑性非牛顿流体在逆流床中的传质进行了研究,结果表明,对非牛顿流体体系,旋转填充床也能大大强化液相的传质过程。
2.4.2 气相控制的传质过程
Ramshaw[30]曾用水吸收氨测定了逆流旋转填充床填料层的平均气膜传质系数,用比表面积为1650的不锈钢丝网填料在760g下得到气膜传质系数为10.8×10-8m/s。朱慧铭[12]也利用水吸收氨体系测定了填料层的平均气膜传质系数,得到加速度与平均体积传质系数及传质单元高度的关系。沈浩[16]等用空气解吸废水中的氨得到传质单元高度为3~10cm。
北京化工大学超重力工程研究中心早期用逆流旋转填充床对水除尘过程进行了研究,结果表明,除尘效率可达99.9%以上,当入口气体含尘50g/m3时,出口气体含尘0.05g/m3,切割粒径0.3μm,达到工业上电除尘装置串联填料洗涤塔的除尘效果。
2.4.3 气液两相控制传质过程
北京化工大学超重力工程研究中心[31]采用水吸收空气中的SO2体系,研究了这个气液两相对传质阻力均有影响的吸收过程。采用安装在旋转填充床填料层不同径向位置的自制电导探头,测定逆流和并流操作条件下旋转填充床填料层内径向的浓度分布。研究了液体流量、气体流量、转速和气相进口中SO2含量四个因素对旋转填充床填料层内径向浓度分布和径向体积传质系数分布的影响规律。研究结果表明。
①逆流旋转填充床填料层内的体积传质系数在填料层的入口处有一极大值,说明在此处为液相端效应区。离开液相端效应区后,体积传质系数随填料层半径逐渐增大,在接近转子的外缘处时,体积传质系数迅速增大,这与液相控制的传质过程相反,说明在填料层的外缘处存在一个气相端效应区。并流时,旋转填充床内的体积传质系数在填料层内缘处迅速增大,说明并流时气、液两相端效应区都集中在填料层内缘处,离开端效应区后,随填料层半径逐渐减小。
②转速和气体流量对旋转填充床填料层内的体积传质系数影响较大,而液体流量和气相中SO2浓度对传质系数的影响不大。
2.4.4 平均体积传质系数实验值的计算
由于气液逆流接触,气液浓度、通量、传质比表面积和流速等沿径向变化,所以很难得到计算床层传质系数的解析式,只能将体积传质系数看成常数,将床层分为微圆环,用试差和递推的方法求取。即先给定体积传质系数Kxa,然后从气相或液相入口端逐层递推,最后求出气液相出口浓度与实验值比较。如果两者之差小于精度要求,则认为Kxa即为所求,否则,修正Kxa重新从头开始递推计算,直到满足要求。
水吸收氨的传质过程是一个典型的气相控制过程,以此为例,建立求取体积传质系数的表达式。
对旋转填充床填料内一个微小的单元层进行物料衡算如下(图2-37)。

图2-37 旋转填充床填料的示意图
根据质量守恒:


将式(2-51)代入式(2-50)得:

对式(2-52)积分:

可得:

令传质单元数,传质单元高度
,则:

H=NTU×HTU
当气相浓度很低时,可用以下方法求NTU:

式中 Y1——NH3在旋转填充床入口的物质的量浓度;
Y2——NH3在旋转填充床出口的物质的量浓度;
Ye1——NH3在旋转填充床入口与液相平衡的气相物质的量浓度;
Ye2——NH3在旋转填充床出口与液相平衡的气相物质的量浓度;
G——为气相摩尔流率;
R1、R2——填料层的内外半径;
H——填料的轴向长度;
a——传质总比表面积;
NA——传质通量;
Ky——液相传质系数。
2.4.5 气液传质过程模型化
根据不同黏度体系中液体微元存在方式,我们建立了相应的气液传质模型,包括适用于低黏度体系(<0.1Pa•s)的变尺寸液滴传质模型[32]、适用于中等黏度体系(0.1~1Pa•s)的表面更新传质模型[33]、适用于高黏度体系(>1Pa•s)的液膜传质模型[34],模拟揭示了旋转填充床内不均匀传质规律。在此基础上,结合化学反应动力学,建立了传质耦合反应过程的超重力多相反应器模型。
2.4.5.1 用于低黏度体系的变尺寸液滴传质模型
以本菲尔溶液吸收CO2为工作体系,进行了低黏度体系传质模型化研究[32]。假设液体在较高的超重力水平下仅以球形液滴的形式存在,在端效应区内球形液滴直径的表达式为:

在填料主体区液滴直径的表达式为:

液滴内组分控制方程:

传质方程:

单位体积内CO2的吸收速率为:

CO2在气相中的质量守恒方程:

利用该模型方程,可在已知气体和液体进口条件的情况下,计算得到旋转填充床出口气体中的CO2浓度。图2-38为计算得到的出口气体CO2浓度(摩尔分数)和实验值的对比图。从图中可知,绝大多数的计算值和实验值的误差都在±10%以内,表明本模型合理。

图2-38 计算值和实验值的对比图
2.4.5.2 适用于中等黏度体系的表面更新传质模型
以离子液体吸收CO2为工作体系,结合基础研究的结果,建立了适用于中等黏度体系的表面更新传质模型[33]。模型假定:
①液体以平推流方式沿填料径向向外流动,液体在填料上有相同的停留时间和流动类型;
②处于填料中的绝大多数液体在高速剪切和填料的撞击下分散成液滴,液滴的总面积即气液有效传质面积;
③在填料空间内,气液为逆流接触,液体每经过一层丝网后浓度就会发生更新。
根据Burns[35]的关联式,RPB内液体持液量为:

根据持液量计算得到液体流速:

液膜每经过丝网一次,即被更新一次,则更新频率为:

根据Danckwerts的表面更新理论,可得液相传质系数:

填料丝网的表面即为气液接触表面,则液相体积传质系数为:

由此建立了以表面更新理论为基础的旋转填充床内气液传质模型。图2-39是液相体积传质系数实验值和模型预测的对比图,实验和模型的偏差在15%以内,两者吻合良好。

图2-39 超重力旋转填充床内液相传质系数实验值和模型预测值对比图
2.4.5.3 适用于高黏度体系的液膜传质模型
以糖浆-丙酮为工作体系,建立了适用于高黏度体系的液膜传质模型[36]。模型假设(如图2-40所示):

图2-40 高黏度体系的液膜传质模型示意图
①液体微元在填料中完全以液膜的形式存在,且能够始终保持连续,直至流出填料;
②流体的体积流量、密度、黏度和温度保持恒定,忽略气相传质阻力和压力变化;
③假设流体从喷嘴喷出后,在离心作用下,以液膜形式运动,其间不断进行着扩散与传质过程,液膜在以后的逐层流动中均被填料丝捕获,并在填料丝表面发生绕流流动;流体在填料内流动时,扩散传质过程只发生于填料空间的无绕丝流动过程。
基于渗透模型,气液相界面上,单位面积的瞬时摩尔传递速率可表达为:

则液膜整个扩散传质过程的传质总量为:

根据质量守恒,液膜整个扩散传质过程的传质总量也可以表示为:

得到扩散传质后流体内丙酮含量计算公式:

因此,丙酮脱除率可由下式表示:

具体计算如下:








在脱挥过程中,高黏体系薄膜在旋转填充床丝网填料内快速流动,无法直接测量薄膜的尺寸。因此,采用前人研究获得的经验公式计算薄膜的长度和厚度。
图2-41给出了真空度对丙酮脱除率影响的模型计算值与实验值,两者吻合良好。
2.4.6 旋转填充床气液传质过程的CFD模拟
为了更进一步理解和揭示旋转填充床中气液传质机制,提出传质强化的优化结构思路。我们采用计算流体力学方法建立了旋转填充床内气液传质过程的二维CFD模型,以真空水脱氧为对象,模拟填料层内气液传质过程,研究各操作参数对传质过程的影响规律,进而提出结构优化方案[37]。
旋转填充床几何模型采用的是正方形来简化填料丝网。正方形以轴心为圆心按一定比例排列成二十层同心圆环,其边长为1mm,两个正方形的中心距为3mm(如图2-42所示)。填料区的孔隙率为0.94,与金属丝网填料的孔隙率0.95相近。整个内圆和外圆被分别设为进口和出口,采用间距为0.5mm的四边形网格进行网格划分,网格总数为164757个。

图2-41 真空度对丙酮脱除率的影响

图2-42 旋转填充床二维几何结构模型和填料区局部放大图
在脉冲速度的求解上,采用较为复杂但更为真实的雷诺应力湍流模型(RSM model)。RSM方程如下:


通过k和ε方程,对RSM方程内原有的脉冲相进行化简



此外,RSM方程中常数Ck=0.09,C1=1.8和C2=0.6,δij是Kronecker符号,可表示为:

k和ε方程分别表示如下:


这两个方程中,常数C1ε=1.44,C2ε=1.92,σk=0.82和σε=1.0。Gk代表的是:

传质过程添加了组分守恒方程组,其中,i组分在q相中的组分守恒方程可被描述成:

式中,D是混合物料中i物质的质量扩散系数,是Sct湍流施密特数,该值被设置为0.7。通过User-Defined-Function(UDF)方法,在组分守恒方程的源项Sc,q中,添加了符合RPB的传质方程。如液相中组分守恒方程的源项Sc,l,根据Higbie的渗透理论可以表示为:

式中,饱和浓度通过亨利定律进行计算,对于水脱氧过程,气相传质阻力远小于液相传质阻力,在式(2-90)中,忽略了气相传质阻力。液相传质系数kLa采用Chen等人[38]提出的经验关联式(2-91)计算得出。这个关联式拟合了多种操作条件下不同物性的液体在不同尺寸RPB内的传质速率实验值,故适用性较高,其表达式如下:

式中,Vi、Vo和Vt分别代表了反应器内空腔区的体积、外空腔区的体积和整体体积,D代表了扩散系数,at代表的是填料的比表面积,ac是离心加速度。
入口设置成速度进口边界条件,由于这是二维几何结构,不适用真实速度,所以速度通过方程式(2-92)得出:

式中,ri是RPB内缘半径,而Z代表了填料的厚度,入口的初始表压设置为0Pa,而湍流强度和水力直径被分别设置为1%和84mm。进料入口的液体分率设置为1。出口为压力出口边界条件,出口的表压设置为0Pa,液体回流量分率设置为0。压力-速度耦合问题通过PISO方法进行求解,体积分率和组分输运方程采用二阶迎风格式进行离散。每个工况都进行1×104步的计算,时间步长为5×10-4 s。
图2-43为旋转填充床在不同转速下液相分布云图。由图可知,在高转速下液体微元尺寸小于低转速下的,提高转速能增加气液相界面,提高传质效率;液相存在分布不均的情况,提高转速可改善液相分布。图2-44表示持液量(εL)及水中氧脱除率(E)的模拟值与实验值的对比。结果表明,持液量的误差在±20%范围内,氧脱除率的模拟值与实验结果的误差值在±10%以内,模型的预测性较好。转速和液量对持液量的影响规律与前人的文献结果趋势一致[35],模拟值均小于实验值,这可能是由于简化填料结构降低了对液体的捕获率所致。

图2-43 填料内液相分布云图(QL=100L/h)

图2-44 模拟值与实验值的对比
图2-45表示溶解氧在填料层内的分布,图2-46表示溶解氧沿径向的分布情况。由图可知,溶解氧的质量分率是随着径向距离的增大而逐渐减小的,根据曲线下降速率可把填料区分成两个部分:一是靠近转子的内缘,称为入口区,至少40%的溶解氧在这个狭小的区域被解吸出来;其余部分称之为主体区,这个区域溶解氧的质量分数沿径向的增加,其下降的速率减缓,在靠近出口区域处,液相中溶解氧的质量分数达到稳定,气液传质过程接近平衡状态。
基于前面的研究结果,可提出结构优化方案。为此研究了填料、转子尺寸以及填料内添加导向板对传质过程的影响规律。图2-47表示了通过改变正方形的中心距Δd来调节填料的参数,Δd值越大表明正方形数量越少,填料的比表面积和空隙率增加。

图2-45 溶解氧的质量分布云图(QL=100L/h)

图2-46 溶解氧沿径向的分布

图2-47 不同填料结构图
图2-48为不同结构填料对溶解氧脱除率的影响规律。结果表明,当操作条件相同时,与Δd大的填料相比,Δd小的填料有更高的氧脱除率,这可能是由于Δd小的填料层具有更高的持液量,液体在该填料中的停留时间增大,对溶解氧的脱除有利。
图2-49表示三种不同尺寸的转子,图2-50为转子尺寸对溶解氧脱除率的影响规律。模拟结果表明,在填料径向厚度一致时,与小尺寸内外径的转子相比,大尺寸内外径的转子在相同的操作条件下有着更大的溶解氧脱除率,表明了大尺寸内外径的转子的气液传质效率更高,这主要原因是由于大尺寸内外径的转子在相同转速下获得了更大的离心力,对液相的剪切作用增强,液体微元尺寸下降,减低了液相传质阻力。

图2-48 不同结构填料对溶解氧脱除率的影响

图2-49 转子不同尺寸示意图
图2-51为添加在填料区内三种导向挡板的结构示意图,图2-52表示在这三种不同导向挡板下转速对解吸率的影响规律。模拟结果表明,角度为-60°导向板的传质效果最好,角度为60°导向板次之,而角度为0°的导向板的传质效果最差,其与常规几何结构填料的基本相同。由于在主体区内液体主要沿径向流动,导向角度为-60°的挡板,其导角方向与填料旋转方向相反,此时导向板改变液体流动方向,提高了液相与液相、液相与填料间的碰撞混合和液体微元破碎,强化了液相传质。