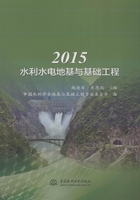
爆破技术及纠偏措施在防渗墙施工中的应用
赵先锋,王玉山,赵俊玲
(中国水电基础局有限公司)
1 概述
大渡河长河坝水电站是大渡河梯级开发中的第10级电站,位于四川省甘孜藏族自治州康定县境内,坝基覆盖层防渗采用二道全封闭混凝土防渗墙,形成一主一副布置格局,墙厚分别为1.4m和1.2m,两墙之间净距14m。主防渗墙布置于坝轴线平面内,通过顶部设置的灌浆廊道与防渗心墙连接,防渗墙与廊道之间采用刚性连接,防渗墙底以下及两岸基岩防渗均采用灌浆帷幕,防渗标准为透水率q≤3Lu。副防渗墙布置于坝轴线上游侧,与心墙底部采用插入式连接,插入高度为9m。
主防渗墙左起桩号(坝)0+11.37m,右止桩号(坝)0+36.47m,轴线全长125.1m;墙顶高程为1462.00m,最大墙深55.02m。副防渗墙左起桩号(坝)0-2.32m,右止桩号(坝)0+131.88m,轴线全长134.2m;墙顶高程为1462.0m,最大墙深56.76m。
根据设计要求及地质资料,地下防渗墙嵌入微风化花岗岩最大深度为4.5m,相邻孔基岩面最大高差为13m,最大孤石直径达到10m;在如此高陡坡、大深度基岩和大孤石中成槽施工难度极大,且成槽质量不易保证,是长河坝水电站防渗墙施工成败的关键问题。
2 本项目施工难点
(1)地层中孤石、漂石含量高,直径大。各个槽段均遇到了孤石堆积层,尤其是左右两岸,开孔就遇到大孤石,在不同深度都遇到了直径超过7m的大孤石,最大孤石直径超过10m;因此加大了孔斜控制难度,同时造成施工进度缓慢。
(2)两岸部位基岩面极为陡峭,最大高差为13m,入岩施工极为困难,工效极低,墙底嵌岩质量难以保证。
(3)漂卵石层架空严重,施工中经常出现漏浆现象,防漏、堵漏需要占用较长的时间,而且容易发生塌孔事故。
(4)地层中的大孤石与基岩均为较完整的花岗岩,岩石的硬度非常高,导致造孔工效很低,且钻具磨损严重。
(5)地下水位较高,施工平台相对较低,槽孔稳定性差。导墙顶部高程为1462.00m,而施工期上游面水位在1461.50m左右,槽孔内外的压力差过小,导致塌孔现象频繁发生,加大了重复造孔工程量;尤其是ZQ-7、ZQ-9、ZQ-19、FQ-9号槽段因大面积塌孔,不得不回填后重新开孔,严重影响工期。
(6)防渗墙施工平台填筑质量较差,碾压不密实,受施工设备长时间震动的影响,槽孔上部容易坍塌。
3 施工设备选择
根据长河坝电站上下游围堰防渗墙施工经验,结合坝基防渗墙地质资料,针对防渗墙沿线孤石含量高、直径大及基岩岩面坡度陡、石质坚硬的特点,项目部开工前组织召开了专题会议研究决定:除钢丝绳冲击钻机外,采用2台XY-2型地质钻机、1台SM-400全液压钻机、2台HM90型全液压履带式钻车参与坝基防渗墙在孤石及高陡坡段基岩中成槽的钻孔爆破施工。
XY-2型地质钻机是一种体积小、重量轻的中浅孔岩芯钻机,钻孔深度100~530m,钻孔倾角0°~90°;它具有轻便灵活、功率大、性能好,通用性强等优点;可用于大小口径金刚石、硬质合金钻头岩芯钻探,也可用于水文、水井等大口径工程施工。
意大利SOILMFC公司生产的SM-400型全液压钻机,全机采用液电控制系统,发动机最大功率108.8kW,最大给进速度4.57m/min。该钻机具有马力强劲、扭矩大、转速调整范围广、移动方便、操作简便、故障率低、便于单机运输等优点。与SM-400型钻机相配套的是TUBEX系列偏心扩孔钻具,该钻具有利于钻机充分发挥效能,其独特之处就是钻进过程中套管始终一同跟进,从而起到护壁的作用。
HM90型全液压履带式钻车采用全液压控制,采用低转速大扭矩马达驱动,动力头与导轨采用新型耐用磨板连接,钻孔角度范围0°~360°。轨道可沿底盘架前后滑移,可左右偏摆30°以及水平上下移动1500mm。该钻车具有结构紧凑、性能稳定、钻进能力强、动力头行程长、钻孔角度范围大、钻进效率高、操作方便、移动灵活等优点;主要用于滑坡治理工程及危岩锚固工程的锚固孔、排水孔、注浆孔施工,也可用于爆破孔和隧道管棚支护孔的施工。
4 钻孔预爆
根据本工程围堰防渗墙的施工经验,确定在坝基主、副防渗墙成槽施工前对地层中的大孤石和陡坡基岩实施钻孔预爆处理。预爆破主要有以下作用和优点:
(1)提前清除了大部分施工障碍,可减少成槽施工中的施工干扰、工时消耗、钻头磨损,缩短了工期,节约了大量成本。
(2)由于钻孔预爆时防渗墙施工平台尚未修建,成槽施工尚未开始,爆破时不会产生任何不利影响;因此爆破孔的布置和爆破参数、措施的选择更为灵活,效果更好。
(3)预爆破孔可兼作补充勘探孔,及时发现地层中孤石的分布情况及基岩面的大概位置,为后续防渗墙施工提供比较详细的地层资料;从而避免了成槽施工中大部分的补充勘探干扰和基岩面误判情况。
钻孔预爆的具体方法是:根据设计地质资料和主、副防渗墙的槽段划分,在每个主孔处采用SM-400型全液压钻机及HM90型全液压履带式钻车钻孔至基岩面位置,然后根据钻孔发现的孤石位置和大小确定爆破筒下设位置和炸药量,准备就绪后自下而上逐段进行爆破。需要处理的陡坡基岩面加密进行钻孔预爆破。
5 成槽施工中采取的措施
5.1 主孔施工
上部回填层和覆盖层中的主孔采用冲击钻机施工,上部8m尽量不抽渣,尽量将上部地层挤压密实,以保证槽孔的稳定性。在施工过程中遇孤石则根据孤石的大小确定爆破处理方式,较小孤石采用“定向聚能爆破”方式进行处理,较大孤石采用“钻孔爆破”方式进行处理;爆破后用冲击钻机继续施工。
主孔钻进至预计基岩面2m以上时开始边钻进边取样,取样间隔深度不超过20cm。钻进至疑似基岩面时,开始采用XY-2型地质钻机钻孔取芯,钻孔深度不小于15m。确定基岩面准确深度后,在钻孔内的基岩上部下设PVC管,然后在管内装入炸药爆破;爆破深度根据基岩面坡比确定,基岩面坡比主要根据先导孔深度确定。
5.2 副孔施工
整个槽段的主孔全部终孔后开始施工副孔。副孔采用冲击钻机钻劈法施工,发现孤石时主要采用“槽内定位、定向爆破”方法进行处理;爆破后用冲击钻头进行冲击破碎,直至基岩面。基岩内的副孔先采用SM-400型全液压钻机或HM90型全液压履带式钻车钻孔爆破,再采用冲击钻机施工至终孔。
对于主副孔之间残留的小墙则采用纯钻法予以清除。若遇硬岩或孤石层则采用定向聚能爆破措施处理。具体方法为:用6寸钢管制作爆破筒,根据孤石分布情况分阶梯布置爆破筒,并用钢筋连接固定,爆破筒按1m间距双向对称布置,并焊接定位管,保证爆破筒正对小墙位置,然后实施爆破。根据地层的稳定性每个爆破筒的装药量为1~3kg。
5.3 高陡坡嵌岩施工
先施工端孔,用冲击钻机钻进,穿过上部回填层、覆盖层后采用XY-2型地质钻机钻孔取芯15m,以确定基岩面的准确深度。先用冲击钻机配十字钻头钻进至基岩陡坡的最高点,再改连续冲击为间断冲击;冲砸出台阶后,下置定位管(6寸排渣管)和定位器(套筒钻头),再用SM-400型全液压工程钻机或HM90型全液压履带式钻车根据基岩面走向及坡度钻爆破孔;钻孔深度控制标准为最高点至少入岩1m。钻孔后根据基岩发育程度及基岩深度确定装药量,一般按2kg/m控制;然后下置爆破筒,提升定位管和定位器进行爆破;爆破后用冲击钻头进行冲击破碎,直至终孔。
其他部位按照0.5~0.7m的距离由浅入深逐渐施工,施工程序与上述钻爆施工方法相同。
6 偏孔的处理
6.1 填块石修孔
陡坡段施工时任意孔每钻进大约1m都要测量一次孔斜,发现孔斜超标时要求立即回填块石修孔。由于主、副防渗墙的墙厚分别为1.4m和1.2m,所以要求填孔块石的直径为0.5~1.0m;回填块石的高度应高于孔斜超标段的最高点。填石修孔的效果一般都比较好,但对于高陡坡段及硬度特别高岩石中的孔斜纠偏不适合采用此种措施。
6.2 定向聚能爆破修孔
主要将聚能爆破筒焊在定位架上,定位架利用螺纹钢筋焊接,并焊接导向筋,然后下至偏孔深度位置,将爆破筒对准斜坡起爆,可取得良好效果。
6.3 浇筑混凝土后钻孔爆破修孔
若孔斜短距离偏差非常大,并且无法利用现有钻孔设备钻孔爆破时,则利用C10混凝土将下部偏孔部位全部浇平(浇筑前要及时将孔底淤积清干净),待混凝土终凝后,利用SM-400型钻机或HM90型履带式钻车钻孔实施爆破。
6.4 导墙上钻孔爆破修孔
若孔内有探头石,根据探头石的位置及大小,可采用在导墙上钻孔爆破的方法处理。由于某些槽段在造孔时出现过大面积塌孔现象,所以在实施钻孔时要求钻孔机组采用跟管钻进的方式。钻孔至距探头石底部约0.5m处,然后下设PVC爆破管至孔底,在探头石上中部装药,装药量控制在0.5kg/m。此种方法效果很好,但若操作不当可能造成孔壁坍塌。
6.5 采用修孔器修孔
若主孔或接头孔发生偏孔现象,则通常利用修孔器来处理。修孔器一般用钢板制作,直径比钻头稍大,加焊到钻头底部,钻头上部加焊导向管。修孔器的工作原理是利用导向装置使钻头对准偏孔处进行冲击削切,以达到纠偏的目的。
7 施工效果
7.1 墙体嵌岩验收情况
经四方地质人员现场验收鉴定,防渗墙墙体入岩深度全部满足设计要求。岩面高陡坡段墙体入岩情况详见表1。
7.2 墙体钻孔取芯及压水试验检查情况
主、副防渗墙施工完成后监理布置了8个墙体检查孔,检查结果表明:墙体混凝土芯样均匀密实,与基岩接触良好;每段压水试验的透水率均小于1Lu,满足设计要求。主、副防渗墙检查孔压水试验结果见表2。
表1 基岩高陡坡段防渗墙入岩施工成果表

表2 主、副防渗墙检查孔压水试验成果表

8 结语
(1)大渡河长河坝水电站位于高山峡谷之中,坝基覆盖层深厚,漂石、孤石含量高,岩面坡度大,地下水位高,上部回填层松散;厚达1.2~1.4m的坝基防渗墙,造孔成槽及嵌岩施工难度极大,极易发生漏浆、塌孔、偏孔、卡钻、埋钻等事故。针对施工难点,在以往经验的基础上,采取了一系列行之有效的措施和最先进的孔内钻孔爆破设备,并加强施工管理,及时调整施工方案及施工工艺,使整个施工过程完全处于受控状态,最终圆满完成施工任务,质量满足设计要求;同时使防渗墙施工技术又上一个新台阶。
(2)在含有大孤石的漂卵石地层中造孔成槽,常用的冲击钻机和重锤已不能完全胜任,必须根据具体情况实施各种形式的孔内爆破。实施孔内爆破时要处理好破碎孤石与孔壁稳定的矛盾;首先要通过各种手段尽可能调查清楚孤石的分布和大小情况,其次是要选择适当的爆破时机、方式、设备、装药位置和装药量。
(3)在高陡坡基岩中进行防渗墙嵌岩施工,较坚硬的基岩单用冲击钻机造孔难以保证施工质量;宜先钻孔爆破,然后再逐孔钻进基岩到预计深度。为保证爆破孔的钻孔质量,钻孔前应下设导向定位装置。基岩中爆破孔的布置、数量有待进一步探索。
(4)坝基防渗墙与围堰防渗墙不同之处是需在基坑中施工,地下水位较高。在此环境下确保槽孔安全和施工顺利主要有两个前提条件:一是施工平台高程不宜过低,二是槽孔划分适当。一般来说,槽孔长度不宜过长,一期槽孔应短于二期槽孔。一期槽孔太长,在频繁爆破的情况下将出现大面积塌孔;二期槽孔太短则在一期槽孔爆破施工时可能导致二期槽孔被击穿形成大槽段,增大施工难度。