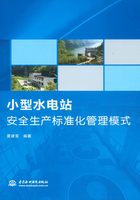
第三节 安全生产标准化
一、安全及安全生产
1.安全
广义安全是指人们未受到威胁或伤害的一种状态,在生产中泛指没有危险,不出事故的状态,是生产系统中人员免受不可承受风险伤害的状态。危险是人们受到威胁或伤害的一种状态,安全是一个相对概念,当危险低于某种程度时,就可认为是安全的。危险是绝对的,安全是相对的。安全是不超过允许限度的危险。
事故(Accident):一般是指造成死亡、疾病、伤害、损坏或者其他损失的意外情况。
事故原因是人的不安全行为和物的不安全状态。
人的本质安全化和物的本质安全化是预防事故的最有效手段。
2.安全生产
安全生产是指在社会生产活动中,通过人、机、物料、环境的和谐运作,使生产过程中潜在的各种事故风险和伤害因素始终处于有效控制状态,切实保护劳动者的生命安全和身体健康。它是保障劳动者在生产过程中安全的一项方针,企业管理必须遵循的一项原则。
3.安全生产管理
安全生产管理是为了达到安全生产目标,在党和政府的组织领导下进行的系统性管理活动,是指管理者对安全生产进行的计划、组织、指挥、协调和控制的一系列活动,以保护职工在生产过程中的安全与健康。
4.安全管理模式
安全管理模式是反映系统化、规范化安全管理的一种方法,是长期积累的安全管理经验与现代安全管理理论与事故预防工作实践经验相结合的产物,包括安全目标、方针、原则、方法、措施等的综合安全管理体系。有以下特征:抓住事故预防工作的关键性矛盾和问题;强调决策者与管理者在职业安全卫生工作中的关键作用;提倡系统化、标准化、规范化的管理思想;强调全面、全员、全过程的安全管理;应用闭环、动态、反馈等系统论方法;推行目标管理、全面安全管理的对策;不但强调控制人行为的软环境,同时努力改善生产作业条件等硬环境。
二、标准及标准化
(一)标准
1.标准的定义
标准指衡量事物的准则,为了在一定范围内获得最佳秩序,经协商一致制定并由公认机构批准,共同使用和重复使用的一种规范性文件。
2.标准的特性
(1)前瞻性。标准是“对活动或其结果规定共同的和重复使用的规则、导则或特性的文件”,不仅反映了制定标准的前提,而且反映了制定标准的目的。同一类技术活动在不同地点不同对象上同时或相继发生,具有重复性,人们根据积累起来的经验制定标准,以便更好地去指导或规范未来的同一种实践活动等。
(2)科学性。制定标准的基础是“综合成果”,单单是科学技术成果,如果没有经过综合研究、比较、选择和分析其在实践活动中的可行性、合理性或没有经过实践检验,是不能纳入标准之中的。同样,单单是实践经验,如果没有总结其普遍性、规律性或经过科学的论证,也是不能纳入标准的,这一规定反映了标准严格的科学性。
(3)权威性。标准是“经一个公认机构批准”的。“公认机构”是社会公认的或由国家授权的有特定任务及组成的法定的或管理的实体,经过该机构对标准制定过程、内容进行审查,确认标准的科学性、民主性、可行性,以特定的形式批准,保证了标准的严肃性,反映了标准发布后的权威性。
3.标准的分类和等级
标准按性质可分为技术标准、管理标准、工作标准;按制定单位不同,可分为国家标准、行业标准、地方标准和企业标准。
技术标准:对标准化领域中需要协调统一的技术事项所制定的标准。
管理标准:对标准化领域中需要协调统一的管理事项所制定的标准。
工作标准:对工作的责任、权利、范围、质量要求、程序、效果、检查方法、考核办法等所制定的标准。
国家标准:如《中华人民共和国标准化工作指南》(GB/T 20000.1—2002)。
行业标准:如水利部发布的《农村水电站技术管理规程》(SL 529—2011)。
地方标准:如吉林省质量技术监督局发布的《水电站管理规范》(DB22/T 133—2007)。
企业标准:如陕西宁强二郎坝水力发电公司《安全工器具管理标准》。
(二)标准化
标准化是指在经济、技术、科学和管理等社会实践中,为在一定的范围内获得最佳秩序,对实际的或潜在的问题制定共同的和重复使用的规则的活动。公司标准化是以获得公司的最佳生产经营秩序和经济效益为目标,对公司生产经营活动范围内的重复性事物和概念,以制定和实施公司标准,以及贯彻实施相关的国家、行业、地方标准等为主要内容的过程。
三、安全生产标准化
1.安全生产标准化概念
《企业安全生产标准化基本规范》(AQ/T 9006—2010)中规定,安全生产标准化是指通过建立安全生产责任制,制定安全管理制度和操作规程,排查治理隐患和监控重大危险源,建立预防机制,规范生产行为,使各生产环节符合有关安全生产法律法规和标准规范的要求,人、机、物、环处于良好的生产状态,并持续改进,不断加强企业安全生产规范化建设。
2.安全生产标准化内涵
体现了遵循“安全第一、预防为主、综合治理”的方针和以人为本的科学发展观,强调企业安全生产工作的规范化、科学化、系统化和法制化,强调风险管理和过程控制,加强隐患排查和治理,注重绩效管理和持续改进。
企业安全生产标准化工作采用“策划、实施、检查、改进”(PDCA循环)动态循环的模式,依据该标准的要求,结合自身特点,建立并保持安全生产标准化系统;通过自我检查、自我纠正和自我完善,进而建立安全绩效持续改进的安全生产长效机制。
四、国家对生产企业安全生产标准化的要求
(1)2004年,国务院印发了《关于进一步加强安全生产工作决定》(国发〔2004〕2号),要求在全国所有工矿商贸、交通运输、建筑施工等企业普遍开展安全生产标准化活动。
(2)2004年,国家煤矿安全监察局颁布《煤矿安全质量标准化标准及考核评级办法(试行)》。
(3)2005年12月16日,国家安监总局颁布《危险化学品从业单位安全标准化规范》(AQ 3013—2008)及考核评级办法和考核评价标准。
(4)2006年6月27日,全国安全生产标准化技术委员会成立大会暨第一次工作会议在京召开。国家安全生产监督管理总局局长在会上表示,全国安全生产标准化技术委员会(以下简称安委会)的成立,标志着我国安全生产标准化专家队伍初步建立,安全标准工作开始步入正常发展的轨道。
(5)2010年4月15日,国家安监总局发布《企业安全生产标准化基本规范》(AQ/T 9006—2010)。
(6)2010年,国务院下发《关于进一步加强企业安全生产工作的通知》(国发〔2010〕23号),要求深入开展以岗位达标、专业达标和企业达标为内容的安全生产标准化建设,凡在规定时间内未实现达标的企业要依法暂扣其生产许可证、安全生产许可证,责令停产整顿;对整改逾期未达标的,地方政府要依法予以关闭。
(7)2011年,国务院安全生产委员会下发《关于深入开展企业安全生产标准化建设的指导意见》(安委〔2011〕4号),要求建立健全各行业(领域)安全生产标准化评定标准和考评体系;严格把关,分行业(领域)开展达标考评验收;不断完善工作机制,将安全生产标准化建设纳入企业生产经营全过程,促进安全生产标准化建设的动态化、规范化和制度化,有效提高企业本质安全水平。
(8)2011年,国务院安全生产委员会印发《国务院安委会关于深入开展企业安全生产标准化建设的指导意见》(安委〔2011〕4号),要求全面推进企业安全生产标准化建设,进一步规范企业安全生产行为,改善安全生产条件,强化安全基础管理,有效防范和坚决遏制重特大事故发生。
(9)2011年5月16日,国务院安全生产委员会下发了《关于深入开展全国冶金等工贸企业安全生产标准化建设的实施意见》(安委办〔2011〕18号),提出工贸企业全面开展安全生产标准化建设工作,实现企业安全管理标准化、作业现场标准化和操作过程标准化。2013年底前,规模以上工贸企业要实现安全达标,2015年底前,所有工贸企业实现安全达标。
(10)国务院安全生产委员会2011年5月30日召开的推进安全生产标准化工作(专题)视频会议提出,要重点做好6个方面的工作:加强组织领导;加强分类指导;加快配套建设,完善安全生产标准化政策法规体系;严格规范管理,形成“四个一批”;加强协调配合,保证联动机制、规划措施、激励政策和监督实施到位;结合“安全生产月”“安全万里行”等系列活动的开展,抓好宣传贯彻,广泛掀起全员标准化工作的热潮。
(11)国务院下发《关于坚持科学发展、安全发展,促进安全生产形势持续稳定好转的意见》(国发〔2011〕40号):(十四)项推进安全生产标准化建设。
(12)2011年,国家安监总局下发《关于印发全国冶金等工贸企业安全生产标准化考评办法的通知》、《关于印发冶金等工贸企业安全生产标准化基本规范评分细则的通知》(安监总管四〔2011〕128号),发布《冶金等工贸企业安全生产标准化基本规范评分细则》,进一步规范了冶金等工贸企业的安全生产标准化。
(13)2013年1月29日,国家安监总局等部门下发《关于全面推进全国工贸行业企业安全生产标准化建设的意见》(安监总管四〔2013〕8号)。提出要进一步建立健全工贸行业企业安全生产标准化建设政策法规体系,加强企业安全生产规范化管理,推进全员、全方位、全过程安全管理。力求通过努力,实现企业安全管理标准化、作业现场标准化和操作过程标准化,2015年底前所有工贸行业企业实现安全生产标准化达标,企业安全生产基础得到明显强化。
(14)2014年修订实施的《中华人民共和国安全生产法》第四条规定:“生产经营单位必须遵守本法和其他有关安全生产的法律、法规,加强安全生产管理,建立健全安全生产责任制和安全生产规章制度,改善安全生产条件,推进安全生产标准化建设,提高安全生产水平,确保安全生产。”将安全生产标准化从行政要求上升为法律要求。
★持续改进的PDCA管理模式(戴明模式):
·P(Planing)——策划阶段。
·D(Do)——实施阶段。
·C(Check)——检查阶段。
·A(Acting)——评审改进阶段。
美国质量管理专家戴明(W.Edwards.Deming)博士,因对世界质量管理发展做出的卓越贡献而享誉全球。20世纪50年代,他作为统计专家被美国政府派往日本工作。他的贡献在于,他发现日本工业界使用的计划—统计—检验方法,并不能很好地解决质量问题。他提出,“要有改善产品和服务的长期目标,而不是只顾眼前利益”、“质量是‘造’出来的,而不是检验出来的。”这种“改善(日文读为Kaizen)”思想,后来成为丰田精益制造模式的精髓。戴明管理理论的特点可归纳如下:
(1)目标—实施—绩效—评审形成一个循环。
(2)理论与实践结合,由原管理水平—达到新的管理水平。
(3)P—D—C—A为一动态管理过程,每一阶段均由P—D—C—A局部动态循环所控制。
(4)P—D—C—A是一个不断提升和不断完善,永远向前,与时俱进的发展,即原水平—新水平—高水平—更高水平……不断提升、不断改进……,有始无终。